Kombination von zwei Schweißverfahren für Dickbleche: Laserhybrid- und Engspalt-Unterpulverschweißen
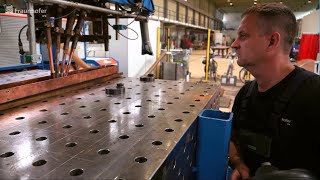
Mit dieser Verfahrensvariante können hohe Blechdicken mit geringerer Lagenanzahl und geringerem Wärmeeintrag hergestellt werden.
Die Laserstrahl-Hybrid-Schweißtechnologie erweist sich in der schweißtechnischen Fertigung mehr und mehr als innovative Alternative gegenüber anderen Schweißverfahren.
Forschende des Fraunhofer IPK entwickeln ein neues Verfahren, bei dem der effiziente Hochleistung-Laserstrahl-Hybrid-Prozess in Kombination mit dem Engspalt-Unterpulverschweißen zum Fügen von dickwandigen Konstruktionen eingesetzt werden kann.
Durch die Kombination der beiden Schweißverfahren werden die Fertigungszeit reduziert und die Wirtschaftlichkeit bei zunehmender Qualität sowie die Wettbewerbsfähigkeit vieler KMU erhöht werden. Auch die Produktivität bei der Fertigung von Türmen für Windenergieanlagen wird deutlich erhöht.
Es weist viele wirtschaftliche Vorteile auf:
Mit dieser Verfahrensvariante können hohe Blechdicken mit geringerer Lagenanzahl und geringerem Wärmeeintrag hergestellt werden. Dies reduziert die Kosten der Nachbearbeitung ebenfalls. Z. B. für das Spannungsarmglühen aufgrund höherer thermischer Belastung der zu schweißenden Werkstücke und der daraus resultierenden Eigenspannungen im Bauteil.
Die einseitige Zugänglichkeit gewährleistet den Verzicht auf teure Handhabungstechniken. Zudem können dickwandige Bauteile bedingt gewendet werden, was ein wesentlicher Vorteil zum Schweißen in Lage/Gegenlage darstellt.
Ergebnis:
Durch die Erweiterung der Produktionstechnologien und den Einsatz neuer Konstruktionswerkstoffe ist nun eine effiziente Produktion möglich. Mit konventionellen Schweißverfahren war dies bisher technisch oder wirtschaftlich nicht realisierbar.