Kaltgasspritzen gilt als eines der modernsten Verfahren im Bereich des thermischen Spritzens. Durch eine Forschungskooperation haben Fraunhofer IPK und IWF der TU Berlin seit neustem Zugriff auf ein hochmodernes Cold- Spray-Fertigungssystem.


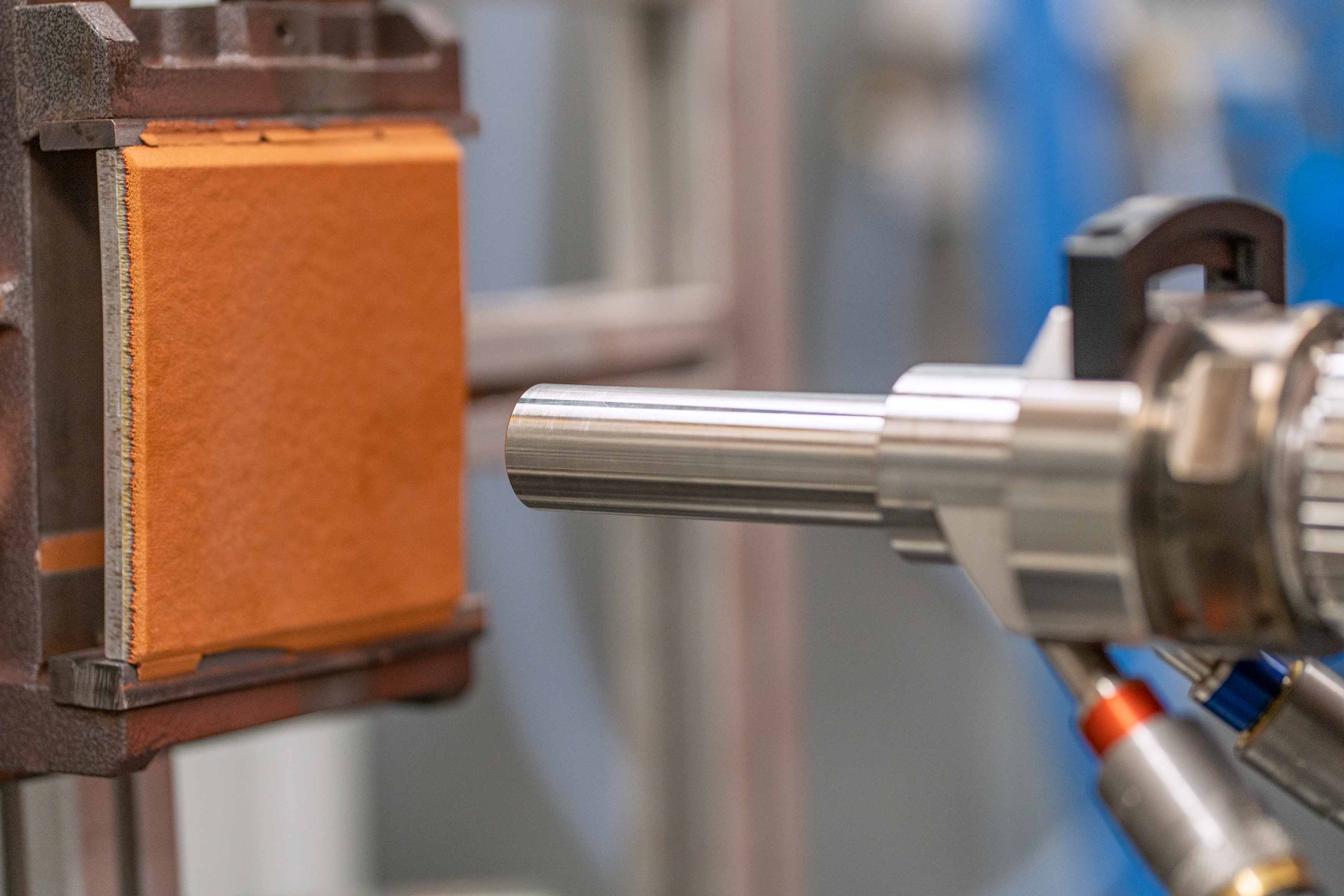
Wer Großbauteile mit komplexen Geometrien, zum Beispiel für den Automobilbau, herstellen möchte, steht vor einer Herausforderung: Der Wärmeeintrag der meisten Beschichtungsverfahren birgt die Gefahr, die Form des Bauteils zu beeinträchtigen – Stichwort Verzug durch Eigenspannungen. Hier bietet das sogenannte Kaltgasspritzen (Cold-Spray-Verfahren) einen innovativen Lösungsansatz: Ein pulverförmiger Werkstoff wird mit hoher Geschwindigkeit auf die zu beschichtende Oberfläche gestrahlt. Durch das hohe Tempo bilden die Partikel beim Aufprall eine feste und widerstandsfähige Schicht. Da das Pulver bei der Verarbeitung eine relativ niedrige Temperatur unterhalb der Schmelztemperatur hat, findet kein Aufschmelzen und Wiedererstarren im Material statt. So können Formabweichungen durch thermisch induzierte Eigenspannungen weitgehend vermieden werden.
Als Ergebnis einer gemeinschaftlichen Investition mit dem Wernervon- Siemens Centre for Industry and Science e. V. (WvSC) steht dem IWF der TU Berlin und dem Fraunhofer IPK seit dem Frühjahr 2023 ein hochmodernes Fertigungssystem für das Kaltgasspritzen zur Verfügung. Ziel ist, mit der Anlage die Grenzen dessen, was bisher mit additiven Fertigungsverfahren möglich ist, zu überschreiten.
Leistungsstarkes Fertigungssystem
Cold Spray ist ein Verfahren der Beschichtungstechnik, genauer gesagt des thermischen Spritzens. Dabei wird ein meist metallisches Werkstoffpulver in einen Trägergasstrom injiziert und durch eine Lavaldüse geleitet. Durch die in der Düse wirkende Strömungsmechanik wird der Gasstrom auf bis zu dreifache Schallgeschwindigkeit beschleunigt, wodurch die Werkstoffpartikel eine hohe kinetische Energie aufnehmen. Beim Auftreffen der Partikel auf eine Substratoberfläche bewirkt diese Energie einen festen Formzusammenhalt.
Man kann sich das Prinzip vorstellen, wie wenn ein Schneeball mit viel Schwung auf einen harten Untergrund trifft: Beim Aufprall wird die Seite, die der Oberfläche zugewandt ist, plattgedrückt, der Schneeball bleibt haften. Träfe nicht nur ein Schneeball auf die Fläche, sondern tausende, entstünde ein ähnliches Schichtgebilde wie beim Kaltgasspritzen. Dabei werden hohe Bauteildichten und ausgezeichnete Materialeigenschaften erzielt. Hierzu zählen eine hohe mechanische Belastbarkeit sowie eine thermische oder elekt-rische Leitfähigkeit, welche durch geeignete Prozessparameter gezielt eingestellt werden können. Darüber hinaus lassen sich durch eine wahlweise seriell oder parallel einstellbare Werkstoffzuführung Materialkombinationen realisieren, die auf dem Gebiet der additiven Fertigung bisher nicht möglich waren.
Kernkomponente des Fertigungssystems am WvSC ist ein Spraykopf des Herstellers Impact Innovations GmbH, der das Trägergas durch einen Druck von bis zu 60 bar und eine Gastemperatur von 1100 Grad beschleunigt. Ein Kuka-Roboter der neuesten Generation bringt den Spraykopf in eine Relativbewegung mit dem zu fertigenden Werkstück. Diese Bewegung definiert, an welcher Stelle der Bauteilgeometrie Material aufgetragen werden soll. Die Reichweite der Robotik ermöglicht dabei Bauteildimensionen von mehr als zwei Metern. Die leistungsfähige Steuerung, die neben den sechs Roboterachsen auch zusätzliche Achsen steuern kann, ermöglicht die Fertigung von Bauteildesigns mit komplexen Geometrien.
Forschung an innovativen Technologien
Aktuell laufende Forschungsprojekte unterstreichen den hohen Innovationsgrad von Cold-Spray-Prozessen. Das Forschungsprojekt »Elektrische Antriebe 2.0«, das in Kooperation mit dem WvSC durchgeführt wird, widmet sich der wettbewerbsfähigen elektrischen Maschine der Zukunft. Die Prozesskette zur Fertigung von großen elektrischen Hochspannungsmaschinen ist bislang durch die Anwendung von konventionellen Fertigungstechnologien geprägt. Additive Fertigungsverfahren bieten die Möglichkeit, geometrische Einschränkungen in der Fertigung von Statorwicklungen sowie Permanentmagneten zu durchbrechen und damit höhere Leistungsdichten zu erreichen.
Im Kooperationsprojekt »AddGleis« aus dem Förderprogramm Additive Manufacturing Berlin Brandenburg (AMBER) des Landes Berlin wird das Cold-Spray-System zur additiven Fertigung von topologieoptimierten Leichtbaukomponenten eingesetzt. Eine leistungsfähige bildgebende Sensorik im Zusammenspiel mit einer KI-basierten Überwachung des Prozessergebnisses wird zur zusätzlichen Weiterentwicklung der Prozessführung beitragen.