A new laboratory allows researchers at PTZ Berlin to experiment with technologies for platform-based production engineering. The aim is to establish a resilient circular economy.
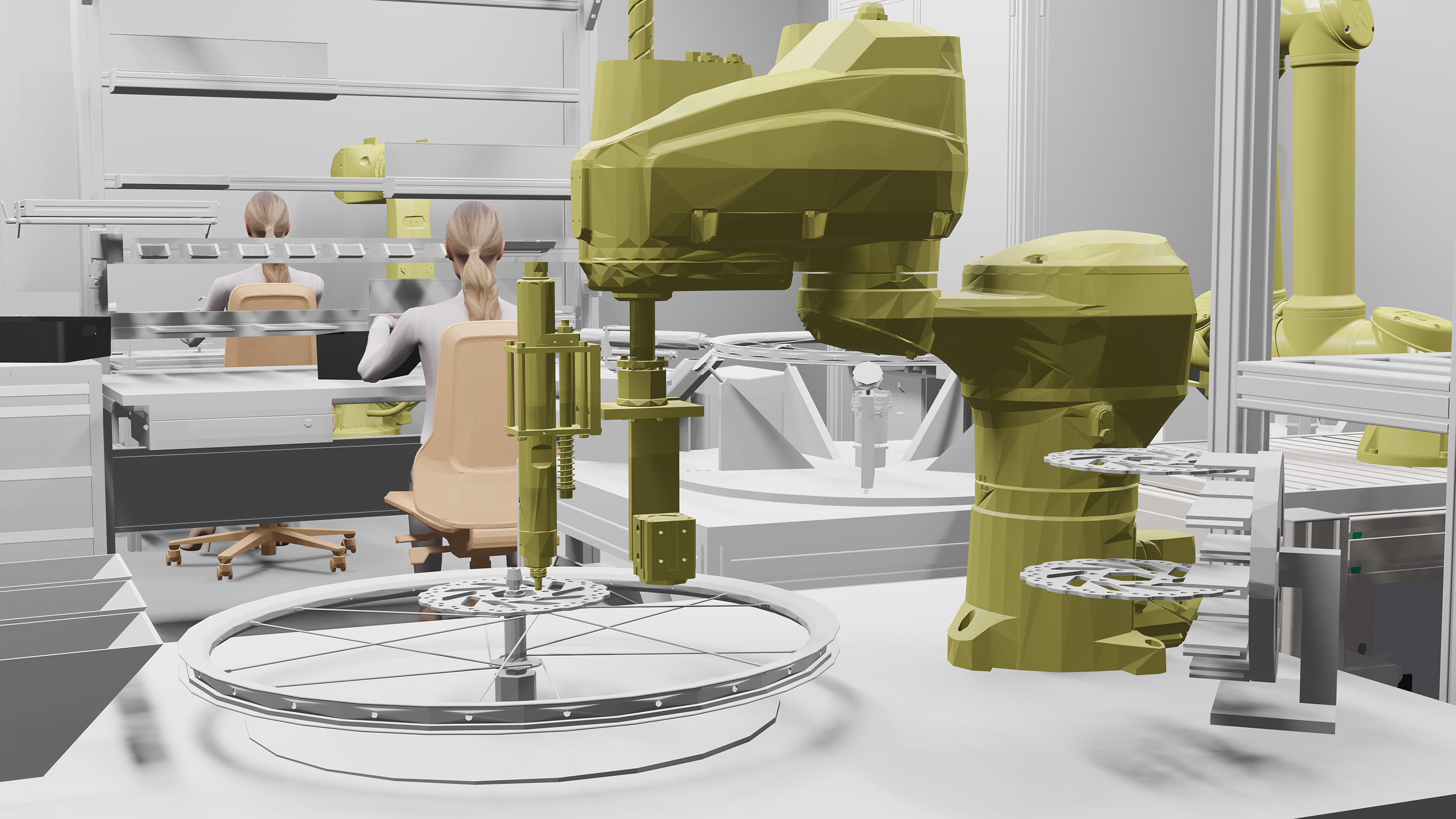
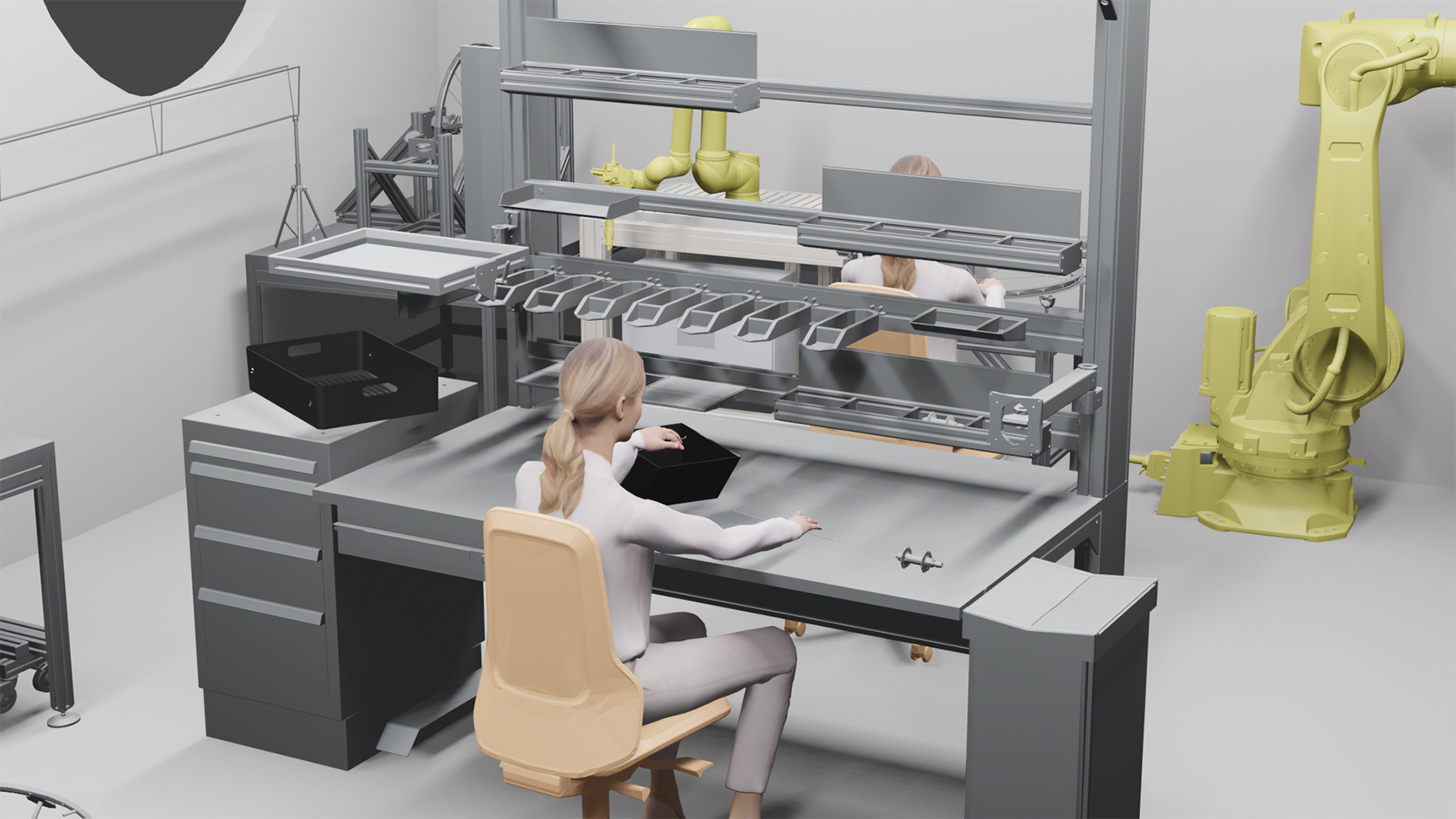
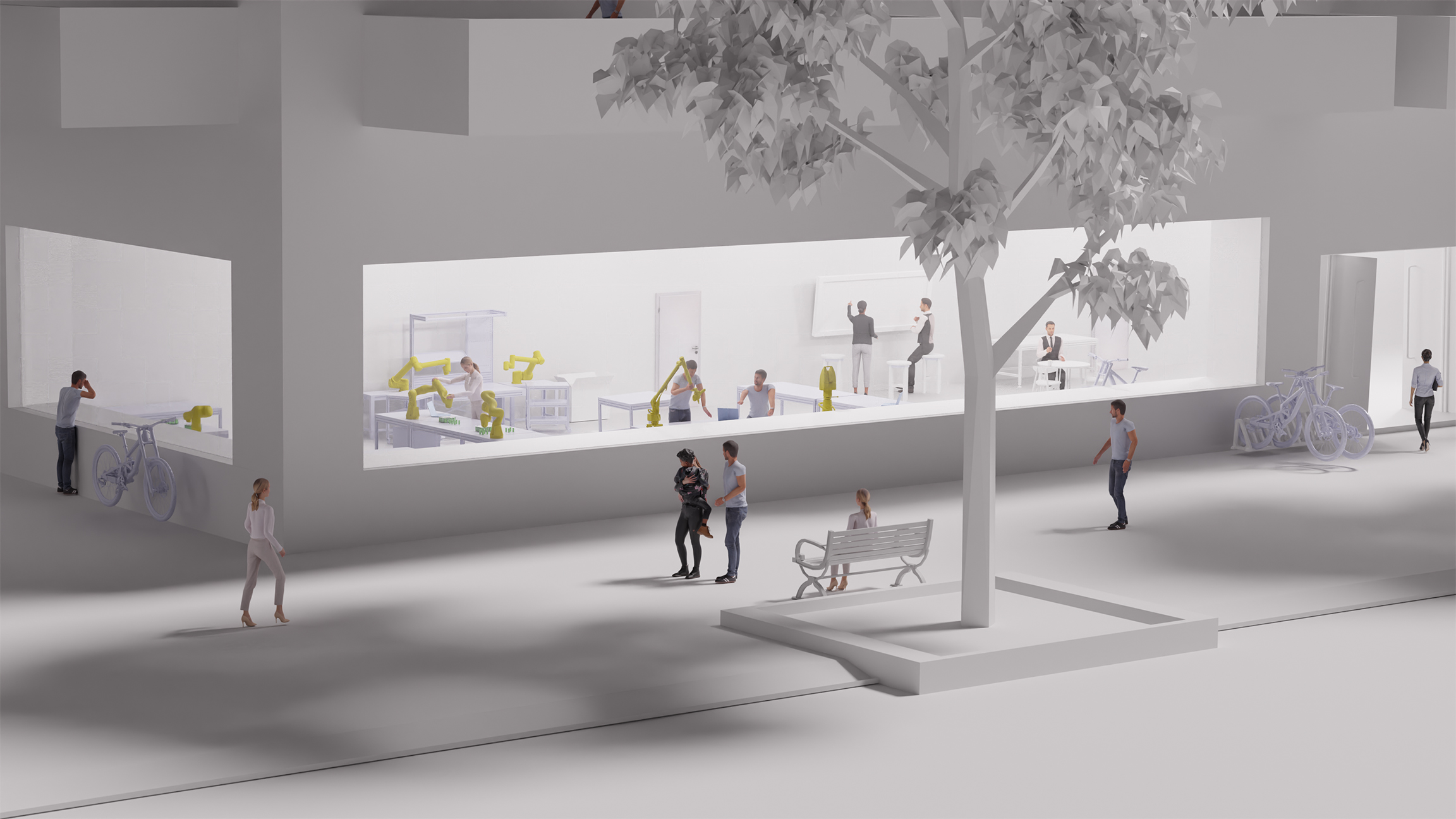
Whether it be mobility, accommodation booking or deliveries, the platform economy has disrupted many established sectors in recent years. This principle connects people or businesses offering goods or services directly to the customer through virtual intermediary and collaboration platforms. The success is based on standardized pooling, efficient linking of previously disparate participants and the wide-reaching nature of platform solutions. This type of economic activity has a number of advantages, such as huge resilience and agility. However, no notable spill-over effects into production engineering have been seen so far: Business models in which production orders are flexibly assigned on a platform basis and collaboratively processed have so far been a marginal phenomenon.
What is keeping manufacturing companies from going down this path is mainly the high levels of required validation and the complexity of the services to be provided. High demand of resources and very specific production expertise are also inhibiting factors. Finally, platform-based processing of production orders requires granularization and order-specific ad-hoc reorganization of operating materials, processes, personnel, and expertise. This remains largely unsolved in practice, particularly in the case of production processes that are more complex than producing individual parts based on drawings.
Scientists at the Berlin Production Technology Center (PTZ) are now working on developing the necessary automation technologies to establish a resilient circular economy based on granularly distributed production resources. The aim is to achieve this by linking cloud manufacturing, handling and assembly technologies as well as services over the entire life cycle and end-of-life processes. To this end, the research team intends to design the relevant hardware, software and data architecture, as well as the methodological conventions, in a highly generalizable, standardizable and automatable way. This reduces implementation costs from the very first site and can be duplicated even more cost-effectively for each additional site.
The »Urban Circular Cloud Assembly and Services Lab (Urban CIRCLAS Lab)«, set up for this purpose, is equipped with industrial robots, cobots, metrology, and safety sensors. The concept is rounded off by shop floor and cloud IT with corresponding digitalization and control interfaces. The laboratory supplements the neighboring manufacturing and automation research labs and maker spaces already in place at the PTZ. For industry collaborations, the Urban CIRCLAS Lab offers an innovative environment where automation and handling technology can be quickly configured with the appropriate shop floor IT.
The scientists are using specific case studies to work on research results and industrializable innovations in the realistic environment of the Urban CIRCLAS Lab. An initial specific example of a project is a twoyear collaboration with Formhand Automation GmbH to develop a camera-free bin-picking approach using soft robotic grippers. The researchers are also planning to investigate automated maintenance and end-oflife dismantling processes for electric vehicle battery systems in the new lab.