Digitally Integrated Production – Fraunhofer IPK Presents Trends for Research and Development
Fraunhofer IPK asked industry representatives what challenges and needs manufacturing companies will be facing in the next few years. The result: Five technology topics will be top priorities across all sectors to ensure manufacturers can not only meet everyday customer expectations, but also manage crisis situations. Digitalization and networking are becoming indispensable keys to success.
We are experiencing a time of profound upheaval. After companies in all economic sectors had to radically change their processes on very short notice due to the pandemic, the next challenges follow on the heels of international conflicts with material shortages and energy bottlenecks. At the same time, companies continue to struggle with a persistent shortage of skilled workers and fierce international competition, which exacerbate cost and time pressures. Not to mention the transformational task that climate change poses for economy and society alike. All these factors are forcing companies large and small to rethink their methods, processes and technologies.
In its role as an R&D service provider with a view to the future needs of industry, the Fraunhofer Institute for Production Systems and Design Technology IPK has conducted background discussions with managers from various sectors in the manufacturing industry. They shared their assessment of the state of technical and methodological development as well as upcoming tasks in their respective sectors. From these discussions, the Fraunhofer researchers have derived research and development needs for five technology topics:
Data Management, Networking and Analysis
Efficient data handling, secure data transmission and intelligent data use take value creation to a new level. Processes can be simplified and accelerated, for example with the help of artificial intelligence (AI) and machine learning. Intelligent process control is becoming a reality, as are adaptive assistance systems that support the handling of variants, quality assurance or machine maintenance.
Manufacturing Systems and Production Control
Data-driven, networked manufacturing brings flexibility to production. Instead of highly integrated, firmly linked lines, manufacturers increasingly favor modular production systems that can be flexibly combined to produce different variants of a product – or different products. Automation solutions address not only production and assembly processes, but also intra-process logistics on the shop floor.
Intelligent Mechatronic Systems Technology
Integrated sensor and network technologies make it possible to continuously monitor the status and behavior of systems and to map them in Digital Twins. This allows processes to be set up more efficiently than ever before. Modern force control and new solutions for human-robot cooperation turn robots into universally applicable processing machines. Machining strategies for new, sustainable high-performance materials are just as much a concern for companies as are primary shaping processes.
Knowledge and Assistance in Production
Highly complex technologies must be made manageable for operators, even if their initial qualifications for handling them are not perfect. Context-sensitive assistance systems provide situational support and secure the know-how of process experts within a company. Technology-oriented training courses, serious games and realistic learning factories teach production management and control methods interactively.
Sustainability and Environmental Compatibility
Slowed-down or closed energy and material cycles in a circular economy help to reduce resource and energy consumption while generating less waste and emissions. An important key here is remanufacturing and refurbishing. At the end of their use phase, products are not disposed of but rather refurbished or broken down into components that can be recycled or even reused.
»In the coming years, a production world will emerge in which all the resources involved – people as well as individual or networked systems – collect data, communicate their status and coordinate tasks interactively«, says Prof. Dr. h. c. Dr.-Ing. Eckart Uhlmann, Institute Director of Fraunhofer IPK. »More and more companies are tackling these challenges with digital methods. This way, a concept is arriving in practice that has been postulated as Industry 4.0 and that we at Fraunhofer IPK call digitally integrated production.« Developing specific solutions and technologies for this together with customers and partners will be the institute‘s top priority in the coming years, says Uhlmann.
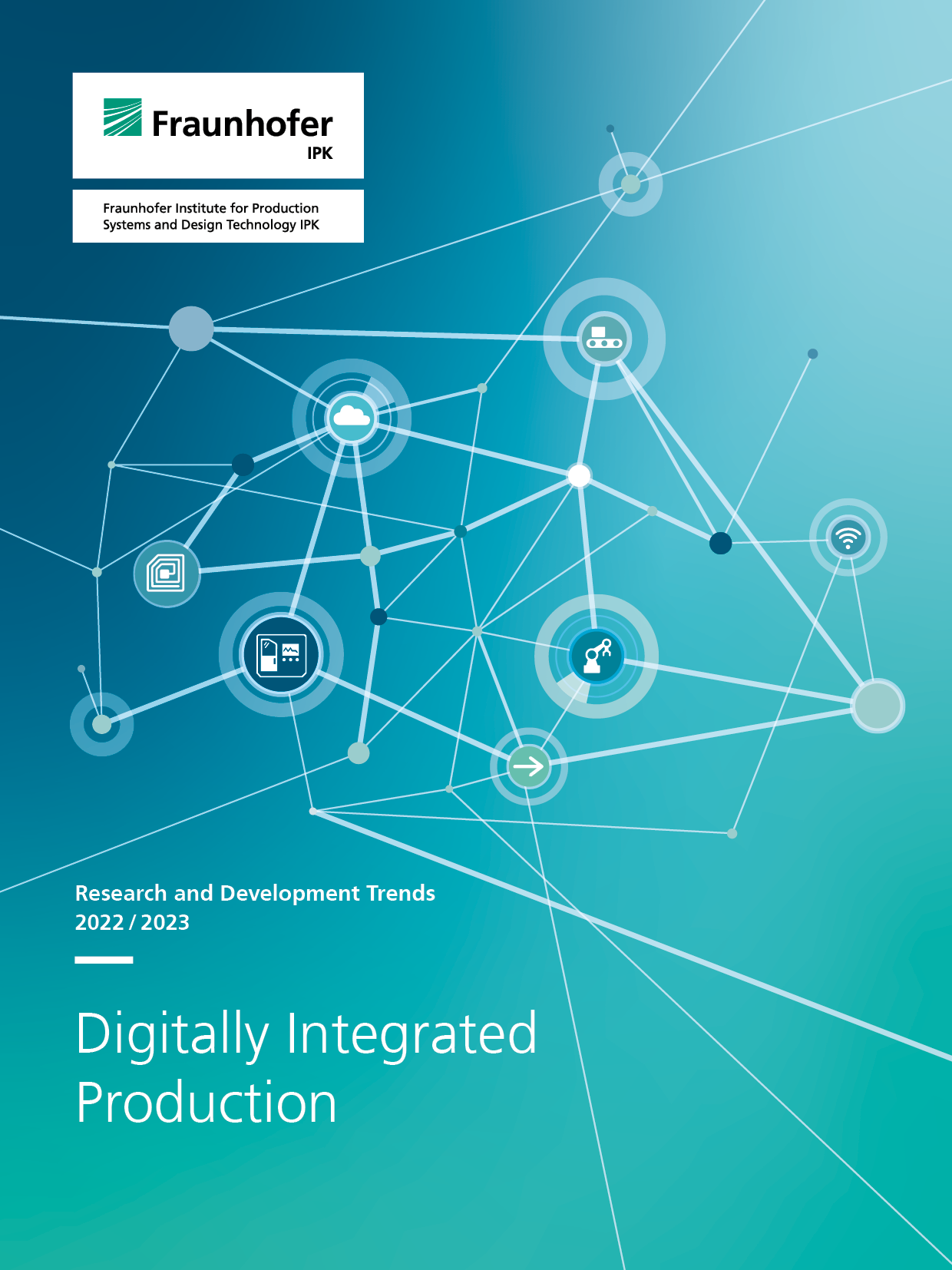