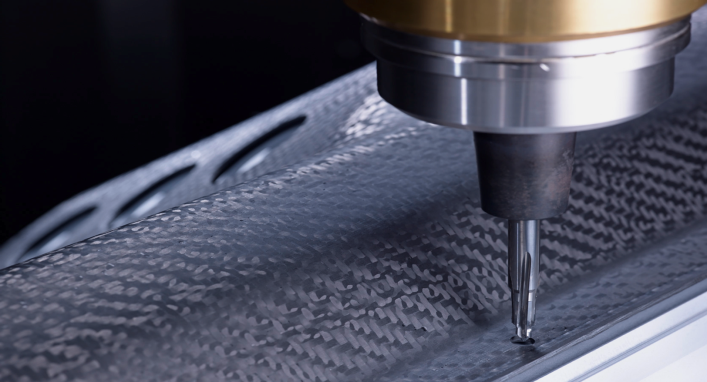
High-performance compression molding and machining of CFRP thick components for structural applications
Over the past decade, global efficiency and sustainability efforts have increased the demand for weight reduction in the transportation sector. Carbon fiber reinforced polymers (CFRP) promise to achieve the desired weight reduction in vehicles while maintaining the desired strength of components. Demand for these materials is therefore increasing, especially in the automotive and aerospace industries. To meet this increasing demand, companies are facing technical challenges in terms of cost efficiency and production volume in the manufacture of high-quality CFRP components.
The main objective of the MAI CompCar project is to develop an innovative process for the production of CFRP components with a thickness of 6 to 8 mm for structural applications. MAI CompCar is divided into two subprojects that are being carried out simultaneously in Germany and Brazil. The aim of the German subproject is to develop and provide a cost- and quality-optimized technology system for the processing of thick CFRP structural components with complex geometries. It also includes the development of high-performance milling tools, optimized machining and cooling strategies and an optical quality control method. The Brazilian subproject, on the other hand, focuses on a previous stage in the production chain of such components, namely the simulation and development of the compression molding of fast-curing thermoset resins. It also includes a non-destructive method for quality control of the molded parts.
Two research institutes, two associations and twelve large and medium-sized companies from Germany, Brazil and the UK are involved in this multinational research collaboration. They all will investigate and add value to the entire manufacturing chain of lightweight CFRP parts for structural applications, from raw materials to quality control. In terms of technological solutions, SMEs typically form the backbone of suppliers to OEMs, e. g. for prepregs and resins, tooling, cutting tools, and manufacturing and quality control systems for composites. In this sense, not only UC members but also other SMEs along this value chain will benefit from the MAI CompCar results, which will be widely disseminated during and after project implementation.