Welding simulation for temperature loading, distortion and cracking
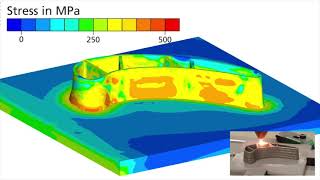
Avoid welding distortion with a simulation. We offer deep insights for your welding processes.
With our welding structure simulation, you will be able to see an individual welding processes (weld, spot) and the behavior of the welded assembly during welding. The simulation model can represent conventional welding processes (resistance spot welding, laser welding, arc welding, etc.) as well as additive manufacturing (e.g. AM-DED).
Our offer for you: Structural simulation for all common welding processes
What to expect?
For a successful simulation you should provide some of your process data.
Minimum requirements
Ideal requirements
Your benefits and advantages: By using our simulation methods, time-consuming and costly experiments can be drastically reduced.