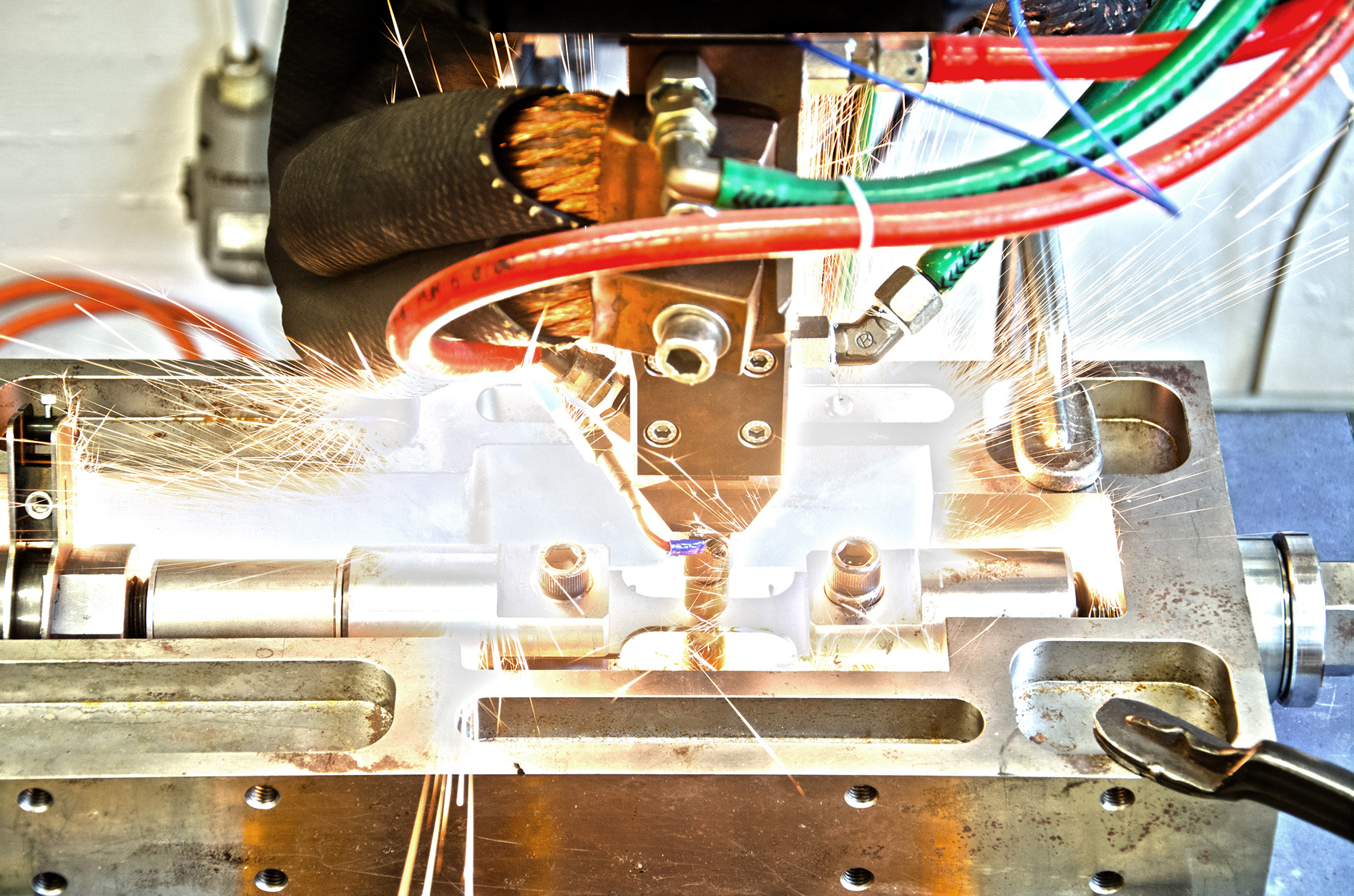
The use of anti-corrosion coated, high-strength steel materials in vehicle construction has increased continuously in recent years. This development is the result of the mechanical and technological properties of these materials that exceed those of conventional steels. High-strength steels can be used to design components with reduced wall thicknesses and thus implement lightweight construction concepts – while simultaneously meeting mechanical requirements. These materials generally have an increased tendency to form cracks during resistance spot welding. This phenomenon is known as liquid metal embrittlement (LME). However, since industry requires crack-free joints, these materials must be qualified for welding applications.
The test setup used in this project (»welding under tensile load«) was able to demonstrate the susceptibility of different zinc coatings to LME. Based on the results, the scientists were able to quantify the influence of the coating on the occurrence of LME cracks and establish an LME susceptibility ranking for the following coatings: zinc-magnesium (ZM), hot-dip galvanized (GI), galvannealed (GA) and electrogalvanized (EG).
In summary, the ZM coatings were found to be the most susceptible to LME, followed by GI and GA coatings. EG was identified as the most LME-resistant coating in terms of frequency and length of the cracks, which the researchers attribute to its higher melting point and the resulting shorter time period in which liquid zinc is available. GI and GA showed a significantly higher susceptibility to LME than EG. The researchers explain this with the additional iron content in these coatings, which leads to a longer availability time of the liquid zinc. The common factor of the latter three coatings is that the LME formation was forced by the external tensile load. In contrast, the researchers observed a continuous occurrence of LME across the range of tensile loads in ZM coatings, indicating that in this case LME cracking was driven by the material properties of the coating. For example, the presence of magnesium in ZM could potentially promote LME crack formation. Additional metallic constituents such as iron and aluminum, which lead to a longer period of liquid zinc availability, are sufficient to provoke LME during welding processes with a low tensile stress level, according to the findings of the project.
The results of this project can be used as a starting point for a material ranking with regard to LME susceptibility. In addition, the determined LME susceptibilities can serve as a basis for concrete recommendations in production engineering applications.
The complete final report is available on the website of FOSTA – Forschungsvereinigung Stahlanwendung e.V. (Research Association for Steel Application, www.stahlforschung.de): Link to final report (in German only)
The research project "Influence of surface coarings on liquid metal embrittlement during resistance spot welding of advanced high strength steel sheets” was funded by the Federal Ministry of Economic Affairs and Climate Action as part of the "Industrial Collective Research" program on the basis of a resolution of the German Bundestag. This project IGF-No. 20812 N / FOSTA-P-No. P1336 from the Research Association for steel Application (FOSTA), Düsseldorf, was carried out at Fraunhofer IPK.