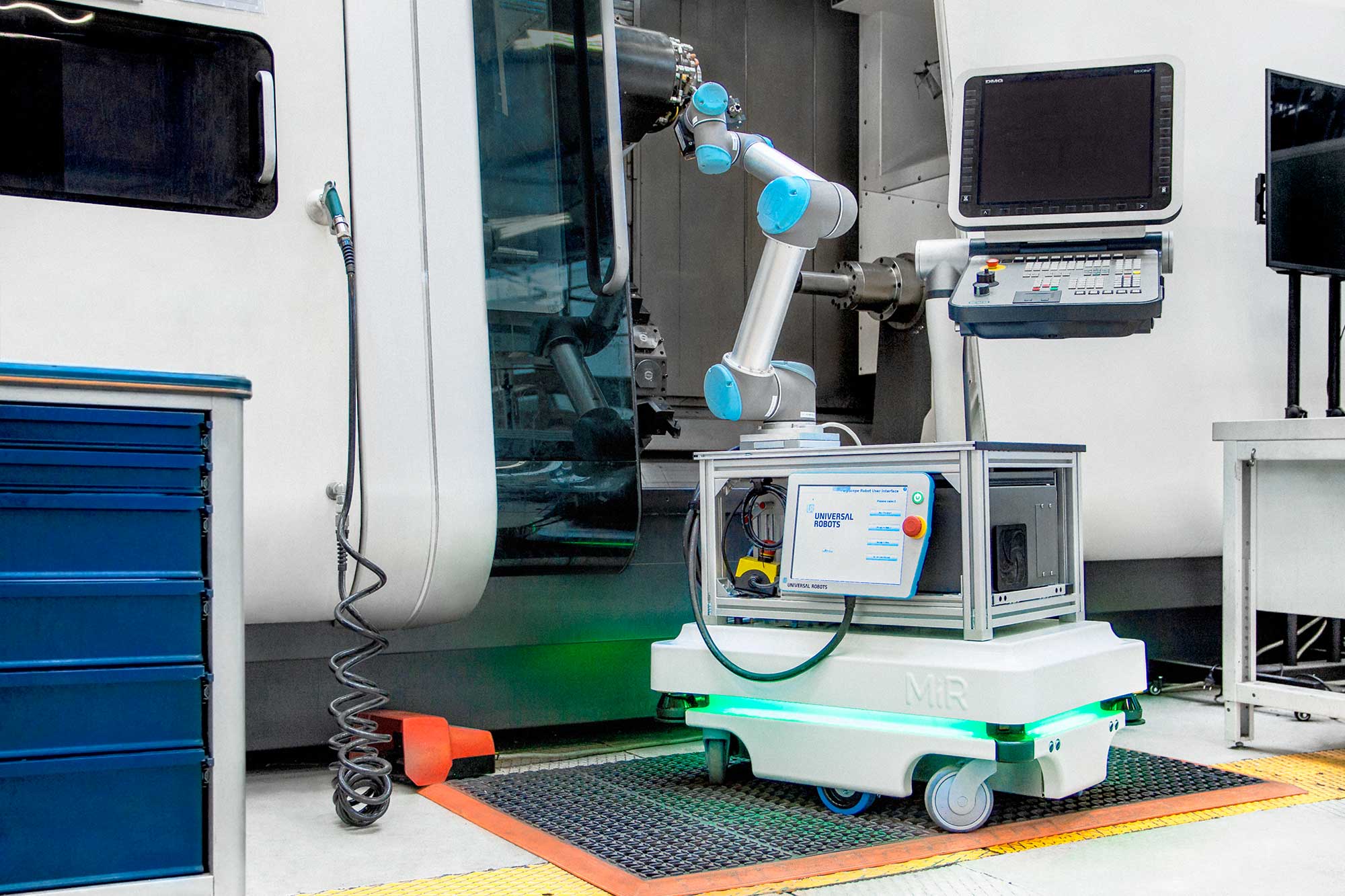
Automated machine tool set-up opens up new potentials
The flexible linking of machines and systems promises higher machine utilization and the ability to respond efficiently to customer-specific orders. In addition to the digitalization and networking of production facilities, this requires more flexible handling and transport technology. In particular, the loading and unloading of machine tools and machining centers ties up human resources in many manufacturing companies that would be better allocated in other fields of activity. Market-ready Systems for automated machine loading are currently only intended for use with stationary robots.
To provide the systems with additional freedom of movement, researchers at Fraunhofer IPK are investigating new approaches to combining automated guided vehicles (AGVs) and industrial robots. Within the Tend-O-Bot project, different machine tools are to be loaded with different workpieces by a mobile robot system. The setup process of the system, which has so far been carried out manually, is to be largely automated.
Fast and precise path planning matters
The AGV is equipped with a robotic arm and provides added value with its transport services. This includes a cloud-based path planning component as well as camera technology and interchangeable grippers. This system allows for machine tending with different workpieces without the need to manually program the robot for each individual job. Even when the workpiece is unfamiliar, the robot can place it correctly using its smart equipment.
While being transported, the workpieces can be measured by the cameras and the path planning for the target machine can be prepared. The trajectory planning depends on the actual positioning of the AGV in front of the machine, as well as on the specific internal space and the fixtures inside the machine. A combination of 2D and 3D camera technology is used to locate the AGV relative to the machine and measure the machine’s interior.
In order to keep the capacity requirements of the on-board computing unit low, the calculation of the robot movements is outsourced. It takes place on powerful computing units such as edge clouds. Due to the centralized structure of the robot controller, several units can be operated simultaneously and the path planning and fleet management for the AGVs can also be outsourced. The trajectory planning for the robot arm can allow different accuracy tolerances between different events. This allows the robot to reorient itself while the AGV is still moving. As the robot approaches the target point, accuracy requirements increase. The tolerances are reduced and the positioning of the robot is refined.